work in process inventory balance formula
On May 1 the company has a balance in Work in Process Inventory of. What Is Inventory Process.
Manufacturing And Non Manufacturing Costs Online Accounting Tutorial Questions Simplestudies Com
The balance sheet would show 4500 in inventory under LIFO.
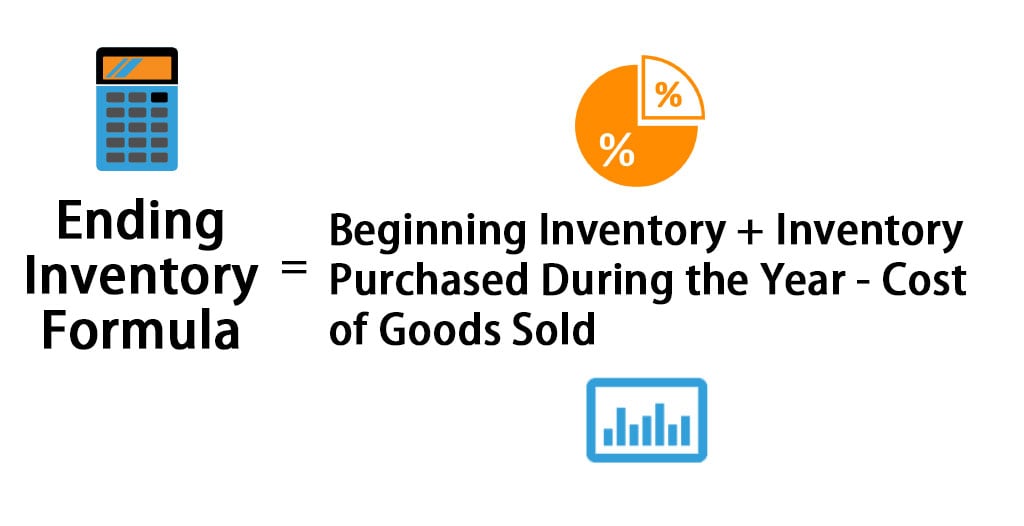
. According to your annual financial statements and accounting records your cost of goods sold is 60000 and the ending inventory is 20000. Since the units are valued at the average cost the value of the seven units sold at the average unit cost of goods available and the. Predict your demand successfully to balance your supply.
Ending inventory using retail Cost of goods available Cost of goods sold during the period. When it comes to efficient inventory management there are many goals to look after. Some of the other reasons behind scrap inventory are.
The difference between the cost of an inventory calculated under the FIFO and LIFO methods is called the LIFO reserve in the example above it is 750. Another method available to calculate ending inventory is the work in process method. The Journal Entry to record Work In Progress Inventory is as follows.
In other words additional processing costs are included in the year-end amount for work in the process too. Work In Progress - WIP. Essentially the inventory process is the lifecycle of goods and raw materials.
This provides the final value of the inventory at the end of the accounting period. Work in Process is one of the three types of inventory with others being Raw Material Inventory and Finished Goods Inventory. Work in process inventory AKA work in progress or WIP inventory is everything that happens to inventory in between raw materials and finished goods.
This includes the cost of raw materials work in process finished goods and any material needs for the ending inventory. Some material is always left that cannot be further utilized in the production process. This reserve is essentially the amount by which an entitys taxable income has been deferred by using the LIFO method.
Its been moved out of its initial warehousing environment and is now a work in progress. Last In First Out is one accounting method for inventory valuation on the balance sheet. This is when the.
Incorporating the right inventory KPIs into your business will help you reach these goals more quickly. It is very difficult for any manufacturing concern to achieve a 100 efficiency level. See a diagram of the inventory process flow and learn more by reading The Essential Guide to Inventory Planning.
Work in progress WIP sometimes referred to as work in process is the sum of all costs put into the production. Statement of Retained Earnings. How to calculate ending inventory using the work in the process method.
An inventory process tracks inventory as companies receive store manage and withdraw or consume it as work in progress. Formula for COGS Essentially to get the cost of goods sold you add the beginning inventory and the additional inventory costs then subtract the ending inventory value. Using Weighted Average Cost Ending Inventory Formula.
Such a process updates your inventory data in real-time sets automatic reorder points avoids double data entry and ensures data. These three balance sheet segments. Work in Process WIP Finished Goods.
Definition Formula Example. Once you conduct the physical inventory you shift the balance in the purchase account into the inventory account. When a company uses low-quality input material it will generate a huge amount of scrap inventory.
Work In Process Inventory. Real-time inventory management is the process of using tools like bar code scanners and inventory management software to record purchases sales inventory and movement of inventory in an online inventory system. A balance sheet is a financial statement that summarizes a companys assets liabilities and shareholders equity at a specific point in time.
Optimize your inventory layout. Refereed to as a work in progress a work in process or a WIP this part of the overall inventory is an asset. Ending inventory retail formula.
You can calculate the cost of ending inventory using either FIFO first in first out or LIFO last in first out. Journal Entry and Accounting Treatment. At that point the inventory is no longer raw.
Finally you adjust the inventory account to match the cost of the ending stock. Reduce storage costs as much as possible.
How To Order Manage Value And Report Inventory Step By Step
What Is Work In Process Wip Inventory How To Calculate It Ware2go
Work In Process Wip Inventory Youtube
How To Calculate Ending Inventory The Complete Guide Unleashed Software
Cost Of Goods Manufactured Formula Examples With Excel Template
Ending Inventory Formula Calculator Excel Template
Work In Process Inventory Formula Wip Inventory Definition
Wip Inventory Definition Examples Of Work In Progress Inventory
What Is Inventory Turnover Inventory Turnover Formula In 3 Steps
Work In Progress Wip Definition Example Finance Strategists
Inventory Formula Inventory Calculator Excel Template
Manufacturing And Non Manufacturing Costs Online Accounting Tutorial Questions Simplestudies Com
How To Calculate Ending Inventory Using Absorption Costing Online Accounting
Ending Inventory Formula Step By Step Calculation Examples
Ending Inventory Formula Calculator Excel Template
Ending Inventory Formula Step By Step Calculation Examples
Ending Work In Process Double Entry Bookkeeping
Solved Calculate The Ending Work In Process Inventory Chegg Com
0 Response to "work in process inventory balance formula"
Post a Comment